Thermal imagers make pictures from heat, also called infrared (IR) or thermal energy. They capture IR energy and use that energy to create images through digital or analog video outputs, with the details defined by differences in temperature. Heat is a separate part of the electromagnetic spectrum from typical visible light. A camera that can detect visible light won’t see thermal energy, and vice versa.
Infrared camera detectors are made of an array of individual detector elements. Because the wavelengths of energy in the IR spectrum are longer than those of visible light, each IR detector element must be correspondingly larger than elements on visible light detectors to absorb the larger wavelength. As a result, a thermal camera usually has a lower resolution (fewer pixels) than a visible light sensor of the same mechanical size. Microthermal cameras, small enough to be in rugged mobile phones, often have a resolution between 80x60 and 160x120 pixels. Thermal cameras used by firefighters and for industrial inspection can have a resolution of 320x256 to 640x512 pixels, providing many times more pixels and significantly better thermal imagery but at a notably higher cost. Co2 Cell Culture Incubator Factory
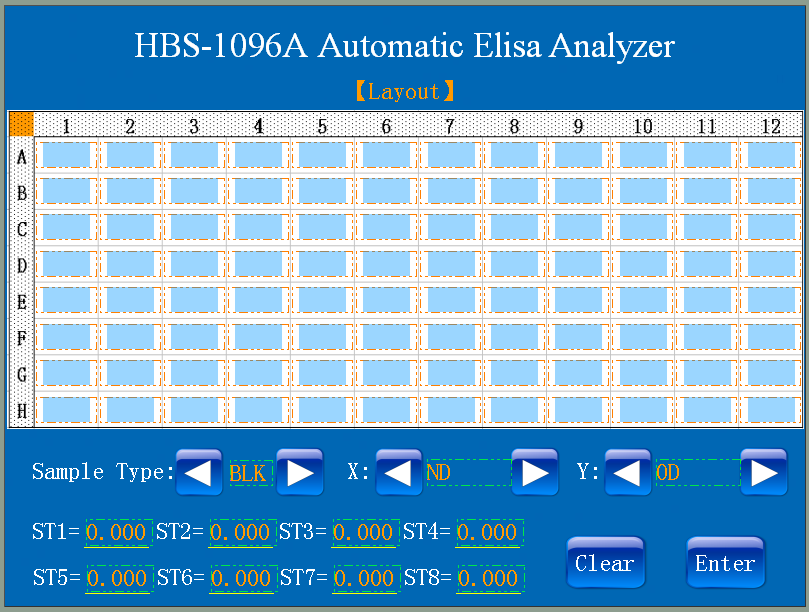
Initially developed for surveillance and military operations, thermal cameras are now widely used for industrial applications such as building inspections (e.g., moisture, insulation, roof, etc.), firefighting, autonomous vehicles, automatic emergency braking (AEB) systems, industrial inspections, scientific research, and much more. These cameras come in a variety of form factors, from handheld cameras to uncrewed drones to scientific instruments sent into outer space.
Engineers developing products or systems incorporating thermal cameras need to clearly understand the critical design specifications, including scene dynamic range, field of view, resolution, sensitivity, and spectral range, to name a few. Different cameras can excel at different things, so engineers need to understand the tradeoffs between different types of thermal camera modules and the impact those differences will have on the final product performance.
One crucial specification often overlooked at the expense of resolution is thermal sensitivity, which defines the smallest temperature difference a camera can detect. A thermal camera’s sensitivity will directly impact the image clarity and sharpness that the camera can produce. A camera with a low NETD probably isn’t necessary if the targets measured typically have wide temperature differences. However, better sensitivity is required for more subtle applications, like detecting moisture issues, security and surveillance, and automotive applications.
Thermal devices measure sensitivity in milliKelvins (mK). The lower the number, the more sensitive the detector. Thermal sensitivity, also called Noise Equivalent Temperature Difference (NETD), describes the smallest temperature difference observed when using a thermal device. The lower the NETD value, the better the sensor will detect slight temperature differences. Integrators and developers should look for manufacturers that can provide NETD performance at the industry-standard 30 °C. A word of warning: cameras from low-cost manufacturers may hide poor sensitivity by taking NETD at 50 °C instead of the industry-standard 30 °C. The table below can be used to rate the sensitivity of a thermal detector generally.
Increased sensitivity makes thermal imagers more effective at seeing smaller temperature differences, especially in scenes with low thermal contrast and when operating in challenging environmental conditions like fog, smoke, and dust. Selecting a more entry-level, essentially lower-cost thermal camera that features “acceptable” to “satisfactory” thermal sensitivity results in an end product that offers low contrast scenes, resulting in poorer image quality, reduced detection range, and limited situational awareness compared to cameras with greater sensitivity. Devices with better thermal sensitivity are ideal for a wide variety of uses, from search and rescue to industrial inspection to security.
To illustrate differences in sensitivity, compare a 50 mK sensitivity thermal camera to a 20 mK sensitivity thermal camera in the images below. The top two images were captured with a 20 mK cooled core camera of a handprint on a wall immediately after the hand was removed from the wall (left), while the right image shows the thermal handprint’s signature after two minutes. Compared to the corresponding bottom images captured with a 50 mK camera, the camera with 20 mK sensitivity can still see most of the thermal signature of the handprint, whereas the less-sensitive camera shows only the partial remains of the handprint. The value of sensitivity is apparent when looking for thermal signatures in such low-contrast scenes.
IR imaging cameras with a cooled detector provide distinct advantages versus thermal imaging cameras with an uncooled detector. A cooled thermal imaging camera has an imaging sensor integrated with a cryocooler, which lowers the sensor temperature to cryogenic temperatures. This reduction in sensor temperature is necessary to reduce thermally-induced noise to a level below that of the signal from the scene being imaged. It can result in significantly improved thermal sensitivity.
However, these performance improvements come at a cost. Cooled IR cameras are generally larger, heavier, and more power-hungry. In addition to sacrificing SWaP (size, weight, and power), cooled cameras are significantly more expensive and subject to mechanical wear and tear that reduces the mean time to failure (MTTF) of the camera, as cryocoolers have moving parts with extremely tight mechanical tolerances that degrade over time, as well as helium gas that can slowly leak through seals. Based on lifetime tests and Weibull analysis, the estimated mean time to failure (MTTF) of the Teledyne FLIR FL-100 cryocooler has increased from approximately 17,000 hours at prototype introduction to approximately 27,000 hours for current production units with a target lifetime of greater than 30,000 hours. This is still significantly lower than the current LWIR camera MTTF.
Recent improvements in uncooled thermal sensors have brought sensitivity to better than 20 mK – a drastic improvement in sensitivity versus legacy systems, potentially making uncooled LWIR cameras a viable option for various new applications. Although tempting, it is essential to note that uncooled IR thermal cameras cannot simply replace cooled thermal cameras. Product developers and system integrators need to consider additional requirements regarding imaging speed, spatial resolution, spectral filtering, and more.
This article was written by Dan Walker, Vice President, Product Management, Teledyne FLIR. For more information, please visit here .
This article first appeared in the November, 2023 issue of Photonics & Imaging Technology Magazine.
Read more articles from this issue here.
Read more articles from the archives here.
Watch a Level 4 Autonomous F-150 in Action
3D Printing a Robotic Hand with Bones, Ligaments, and Tendons
How Much Do You Know About Jet Engines?
Scientists Amplify Superconducting Sensor Array Signals Near the Quantum...
5Ws of the Edible Battery
How Much Do You Know About DC Power Supplies?
Here's an Idea: A New Minimally Invasive Approach to Spinal Cord Injury
NVH Prediction in Electric Powertrains: Considering Inverter and Motor Spatial Harmonics
Understanding Technological Advancements in IR Detection Modules
The Path to ISO/SAE 21434 Cybersecurity Compliance
Here's an Idea: Human Factors in Drug Delivery
10 Tech-Savvy Holiday Gifts for Engineers
Laser Setup Probes Metamaterial Structures with Ultrafast Pulses
Answering Your Questions: Lithium-Air Battery vs. Lithium-Ion
AI Steers Adaptive Control Systems
Comparison Between Wave Soldering and Reflow Soldering
Printed Electronics: The Future Is Flexible
Polycarbonate Seen As Top Choice for LED Lighting
MIT Engineers Design a Robotic Replica of the Heart’s Right Chamber
The Modern Industrial Workhorse: PID Controllers
The Basics of Encoder Selection
AI Helps Robots Manipulate Objects with Their Whole Bodies
Smart Sensor Technology for the IoT
Networking the IoT with IEEE 802.15.4/6LoWPAN
Contact-Free 3D Hybrid Printing with New High-Performance Materials
Laser Beam vs. Electron Beam Welding Which process works best for what?
‘Digital Winglets’ for Real-Time Flight Paths
Mechanical Carbon Materials for Aircraft Seal Applications
Brushless Motors for In-Tank Fuel Pumps
Here's an Idea: A New Minimally Invasive Approach to Spinal Cord Injury
Here's an Idea: Human Factors in Drug Delivery
Here's an Idea: Powerful Sensors for the Eye
By submitting your personal information, you agree that SAE Media Group and carefully selected industry sponsors of this content may contact you and that you have read and agree to the Privacy Policy.
You may reach us at privacy@saemediagroup.com.
You may unsubscribe at any time.
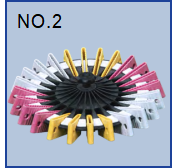
Microplate Reader Manufacture © 2009-2023 SAE Media Group